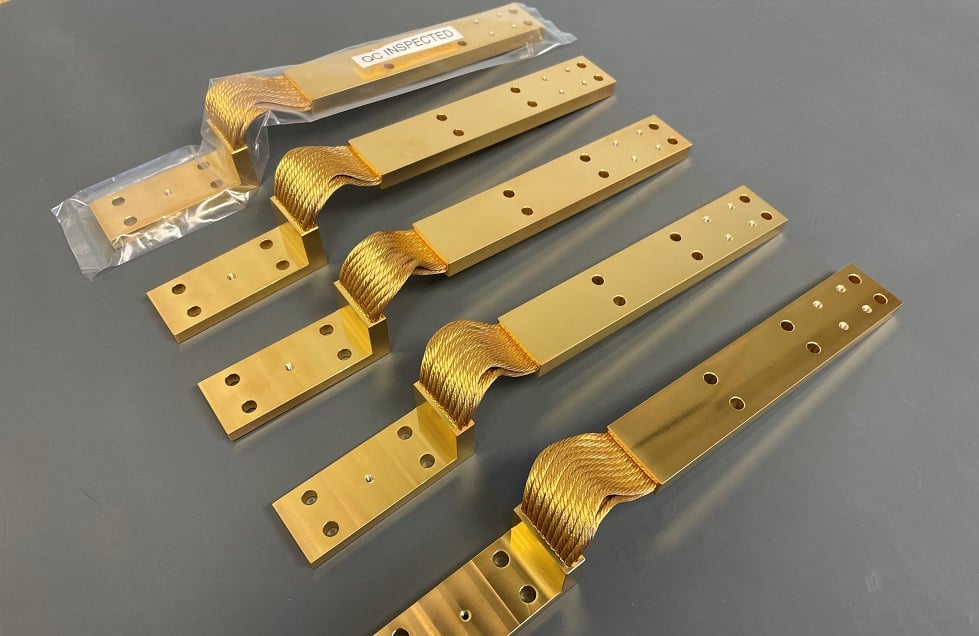
Copper Thermal Strap Design & Ordering Tips
With the surge in business in the last few years, the Design Engineering team and I are starting a new series of blogs based on design tips, best practices, and common questions on our thermal strap products. In today's post, we cover some basics and helpful tips for engineers when beginning your Copper Thermal Strap (CuTS®) design program.
![]() |
![]() |
First, and most important: TAI provides all front end thermal strap design at no charge for every customer. While you are of course welcome to design your own strap, and our team is happy to provide you with STP files of standard models and design advice, understand that the most efficient path forward is to simply provide our team with a completed questionnaire and STP files detailing the heat source and sink, and available envelope (complete with keep-in zones and any obstacles within the envelope). With that information, either of our Design Engineers can model up a notional thermal strap design in a matter of 1-5 business days (depending on complexity and the number of customers in our queue).
Question: if TAI provides design at no charge, how do you recover the cost of days, weeks, or even year's worth of design time (as can be the case with satellite and commercial crew vehicle programs that can take 1-3 years to finalize, due to changes and delays from NASA or aerospace prime contractors)?
Answer: simply put, we don't. TAI is dedicated to providing thermal straps at the most affordable price in the industry, and it was this commitment to affordable pricing, standardization, and in-house design and manufacturing that allowed us to become the largest supplier in the world (and never charging $5,000 - $10,000+ per unit for a metallic thermal strap, as our competitors do). That being said, with each program there are several hundred dollars worth of NRE to cover the price of custom fixturing and machine setup and breakdown that are required, and for (some) fully custom and complex strap designs, this can exceed $1,000.
Copper Thermal Strap Design Parameters
The following tips are based on our copper thermal strap manufacturing process, and are important factors to consider when first designing a thermal strap for any application:
Bolt Hole Keep-out Zones
TAI swages our CuTS® to preserve the flexibility of the cabling. As a result of this cold press process, bolt holes are not drilled through the swage zone. Standard and custom models using our 0.10 inch diameter OFHC UltraFlex I cabling typically require a rope insertion depth ranging from 0.35-0.45 inches. Standard and customs models using our 0.20 inch diameter OFHC UltraFlex II cabling typically require an insertion depth of 0.50 - 0.80 inches depending on rope length and model. Note that these are general rules of thumb, and some custom designs may require different keep-out zones. When designing your thermal straps, please be sure to keep bolt patterns behind the lines, and generally to the back half of the fitting when possible.
Number of Ropes Per Row and Maximum Number of Rows
TAI only swages straps with 1 or 2 rows of cables, as adding a third or fourth row of cables significantly increases stiffness. However, OFHC UltraFlex II cabling allows us to offer the equivalent of a 4-row strap (using UFI), without this stiffness penalty. If your application requires more performance, we can stack straps, use a custom design, or reduce the rope length to increase the thermal performance. Additionally, all straps must have a minimum of 3 cables per row.
Copper Cabling Bend Radius
When planning your design, assume a 0.50 inch (12.5mm) minimum bend radius for all straps.
Installation Configuration is Key with Double Row Thermal Strap Designs
If your application requires a double row standard or custom design, and the strap is to be installed in a curved configuration (L, C, U-shape), the outer row of cables will need to be made longer than the inner, to optimize flexibility and avoid potential damage to the strap. In these cases, TAI will require an STP file detailing your interfaces and envelope to properly model the appropriate rope lengths. In most cases, this will mean an outer row of cabling that is between 0.25 - 0.50 inches longer than the inner row.
90º Lateral Routing Changes
We often come across strap designs from customers in which the cabled section of the strap makes a 90 degree left or right turn on a flat surface (where the heat source and sink are perpendicular to each other), meaning each cable in a given row will need to be made a fraction of an inch longer than the cable before it. These configurations are extremely difficult to manufacture and inefficient. As an alternative, our Design Engineers will instead extend the length of the solid fitting material to incorporate any 90 degree bends, so that a shorter length of straight cabling can be used. This not only simplifies the swage fixturing and assembly process, it dramatically improves the thermal conductance by reducing the rope length and making up the gap with solid material.
Minimum Rope Lengths
Thermal straps are meant to be flexible and provide vibration attenuation/isolation, and copper cabled straps offer exponentially greater flexibility than their foil counterparts. But if your rope length is too short, they can become just as stiff as equivalent metallic foil straps, and even become impossible to manufacture. For single row straps using our OFHC UltraFlex™ I cabling (UFI), the minimum rope length (that is, the length of the rope between the fittings--not including the portions that are inserted into the fittings) is 0.50 inches (12.7mm). For double row UFI models, the minimum rope length is 0.90 inches, or 23mm. For our larger UltraFlex II models and custom designs, the minimum rope lenght is reduced to 2.25 inches (57mm).
Rope Length (RL) and Bolt Pattern Customization
With all of our CuTS® products, the rope length and bolt pattern customization is free--with a few exceptions. Straps that have an RL of longer than 18 inches (457mm), or that have bolt patterns that require helicoil inserts, will have a small additional charge. It is also important to note that since the pandemic and supply chain issues started in 2020, there has been a worldwide supply shortage of certified nitronic and bronze helicoils. This has led to program delays for parts requiring these inserts. Stainless Steel inserts are much more common and there are no supply chain limitations.
Gold and Nickel Plating Your Thermal Straps
TAI offers gold and nickel plating of our copper straps. Plating typically adds 4 weeks to the lead time, and can cost between $200 - $1,000 per unit depending on the design, amount and type of plating material required, and the quantity. It is important to note that there is no benefit or cost savings in only plating the fittings vs the entire strap. In most cases, the amount of tech labor time that is required to properly mask off and prep straps so that only the fittings are plated, is roughly equivalent or even more expensive than simply plating the entire assembly. Plating just the fittings will also lead to a small amount of plating material wicking up the cables on each end, and will leave a noticeable color stain/change trail of 0.25 - 0.75 inches (even with the best masking job).
Also note that we cannot alodine coat a copper thermal strap, nor can we plate the fittings prior to final machining (which removes excess material and adds bolt patterns), as the coating will simply be removed along with the top layers of copper.
We hope that helps, and stay tuned for more design tips coming soon for our PyroFlex™ and Graphene Thermal Straps next month!